**Please note this article is part of a larger series that was first released in the January 2021 Monthly Playbook.
In the world of manufacturing, things move quickly. The manufacturer’s goal is to manufacture their product with the target quality in the proper quantity with as little waste possible. Many manufacturing outlets will do their quality control before a process starts and after the process ends, but what about while something is being created?
Cannabis Manufacturing for the 21st Century
Part 2: Process Control in Cannabis Manufacturing
In the world of manufacturing, things move quickly. A manufacturer’s goal is to manufacture their product with the target quality in the proper quantity with as little waste possible. Process control is actively monitoring your processes so that you can react quickly to control your system if something goes wrong.
Many manufacturers have implemented or are looking to deploy analytical techniques to assess not only the incoming and outgoing goods, but also throughout the processes that transform the raw materials into those final goods. Many basic process tanks monitor simple things, such as temperatures and pressures of all the lines and tank, to help ensure safe working conditions. However, many industries, have moved to putting in more complex technologies so that they can monitor the actual chemical processes that are occurring in their tank.
A first step towards understanding a process is to “thief” samples during the process and measure various characteristics of interest (i.e. cannabinoid concentrations, solvent concentration, water content, etc.) in a lab. This helps to get an idea of the progress and performance of a process; however, there are numerous pitfalls associated with this method. The first pitfall is that someone has to physically retrieve a sample from the process.
Unknown Outliers [1]
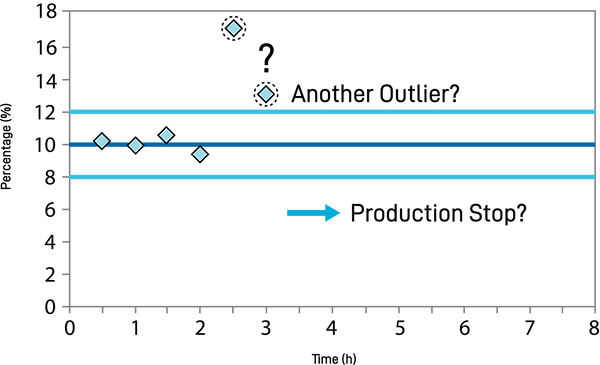
This can be a simple and easy task, but it can also require major safety precautions and training for all personnel. On the way to the lab, there is ample opportunity for the sample to be contaminated or to morph as a result of the different environment of the carrying container. Finally, to turnaround test results from the lab may take hours to days to weeks, depending if the lab is on-site, local, or remote. What happens to the process if the tests take an hour, or twenty-four, to give the users a result they can act on? A second sample would have to go through the same process, doubling the time needed to make an effective decision of whether or not to stop the production (Figure 1).
Potentially, a manufacturing site could wait weeks to confirm that their products pass Quality Control and can be shipped to their customers. In a process that can have thousands of gallons of sample every second, it can become problematic if the manufacturing site needs to wait even a few hours to get the results from a thieved sample.
SCHEMATIC OF A PROCESS TANK [1]
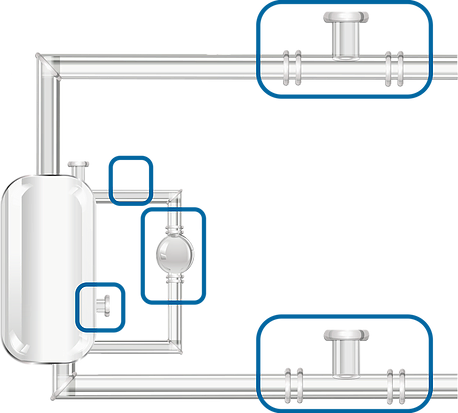
Older industries are slow to move to some of the newer technologies for numerous reasons. In the pharmaceutical industry, a change in the process of the manufacturing of drugs requires months, perhaps years, of investigating and validating the change. Even for a large pharmaceutical company, this can be a serious strain on resources. Thus, most pharmaceutical companies will not accept any changes unless they absolutely are
forced into the change. Other reasons are that certain technologies have only caught up to the monitoring speeds that are necessary. In a standard process tank there could be numerous inlets and outlets (see Figure 2). Each of these inlets and outlets can have several points where monitors and controls can be added to the process.
Properly specified sample interfaces allow a spectroscopic sensor to be installed directly into the manufacturing stream to collect data as the process flows past the sensor. These
sensors give a user real-time information on the conditions within their process.
Spectroscopy allows monitoring of the chemical species within the process, and it can be apparent very quickly if an unwanted side-reaction is occurring thereby allowing the user to react and adjust the process. Beyond the value of instant insight, advanced process sensors also give the benefit of big data aggregation, where additional efficiencies and optimization can be gained over time as well. The ultimate goal is to create a control solution that is constantly monitoring the entire system, so that it can proactively, and automatically, change a parameter if something starts to go wrong. This automated
learning would allow for a fully autonomous system that is efficient and safe.
In the next installment of this series, we will begin exploring the benefits of spectroscopy for the inline monitoring of the various stages of manufacturing in the cannabis industry.
References:
- S. L. Carrier, Impact of Emerging Tools for Process Control, Bethesda: IFPAC 2018 Conference, 2018.